The U.S. Vinyl Industry’s Sustainability Initiative Is Rooted in Past Innovations
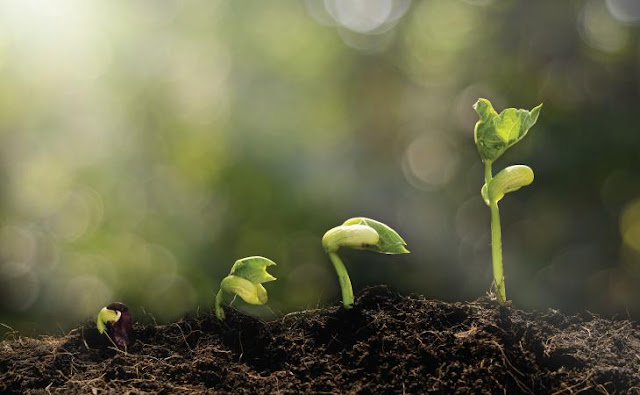
The U.S. vinyl industry is engaged in a comprehensive, sustainability strategy that began in 2016 with the formation of the Vinyl Business and Sustainability Council and the launch of a materiality assessment to obtain an overall snapshot of stakeholder perceptions about how the industry is doing in the environmental, social, and economic spheres—and where it can do better.
While attention is being put on this and other current sustainability initiatives, what often gets overlooked is that the U.S. vinyl industry has in fact been focused on driving innovation and sustainability for almost 50 years. Here’s a snapshot of that effort and the results that came about in reducing emissions, eliminating harmful chemicals, and making workers safer.
A Culture of Safety
Resin production has increased significantly since the 1970s – and yet, at the same time, emissions have been reduced and on-the-job health and safety has been strengthened considerably. In fact, many resin manufacturers have had five or more years with zero OSHA recordable occupational injuries or illnesses resulting in medical treatment.
This culture of safety began in earnest in the 1970s when resin manufacturers made significant innovations in the vinyl resin industry. Resin manufacturers moved to a process of closed-loop manufacturing, which eliminated exposure for facility workers. By implementing technological advancements in resin production processes, the vinyl resin manufacturers not only made the entire process more efficient, but they also made improvements leading to cleaner air and water.
Smarter Resin Manufacturing
The vinyl industry also has made continuous improvements in the resin itself. Capital investments in equipment have led to innovations in stripping out practically all the vinyl chloride monomer from the resin. This further reduced exposure to workers downstream who use the resin to create products. Meanwhile, the vinyl chloride that is stripped out is recovered and reused in the resin manufacturing process, creating efficiencies and reducing waste.
Another area of improvement is in chlorine production, which is one of the building blocks used to make PVC resin. U.S. and Canadian resin manufacturers produce their own chlorine at or near their PVC resin facilities. This self-reliance for chlorine production minimizes the risks associated with chemical transportation and leaks from loading and unloading operations, and also reduces the industry’s carbon footprint and increases worker safety.
The industry also no longer relies on mercury-cell technology to produce the chlorine used in PVC resin. Today, U.S. resin manufacturers rely on chlorine produced using either diaphragm technology or membrane-cell technology process, which eliminates their reliance on mercury.
Elimination of Heavy Metal Stabilizers
The invention of alternative stabilization technology eliminated the need for stabilizers that contain metals, such as lead or cadmium. This technology was commercialized and has been used in the United States and Canada for the past three decades. In addition, U.S. vinyl products manufacturers have led the way on this stewardship effort on a global basis.
Like the vinyl industry’s current sustainability initiative, its roots in past innovations extend from resin manufacturers to product manufacturers. The latter have also made great strides in designing and building better vinyl products.
Original Article from Vinyl Info: http://www.vinylinfo.org/news/us-vinyl-industry%E2%80%99s-sustainability-initiative-rooted-past-innovations
"Thank you so much for sharing this useful information, Keep sharing this kind of information
ReplyDeleteBest Interior Design Company in Bangalore | Home Interiors | Modular Kitchen | Bedroom "